Unknown Facts About Alcast Company
Table of ContentsSome Known Facts About Alcast Company.Fascination About Alcast CompanyThe Of Alcast CompanySome Ideas on Alcast Company You Need To KnowLittle Known Questions About Alcast Company.See This Report on Alcast CompanyHow Alcast Company can Save You Time, Stress, and Money.

If you assume that a wrought alloy may be the very best for your project, have a look at several of our write-ups that explain more regarding details functioned alloys, such as Alloy 6061 and Alloy 6063. On the other hand, if you think a cast alloy would be much better for you, you can find out a lot more regarding some actors alloys in our Alloy 380 and Alloy 383 write-ups (coming quickly).
The Best Guide To Alcast Company

Having the experience and industry knowledge to engineer your castings for optimal production and quality end results will certainly streamline the project. Producing light weight aluminum spreading calls for a facility collection of procedures to attain the appropriate outcomes. When picking a new aluminum foundry to companion with, guarantee they have considerable industry experience and are well-informed about all aspects of the aluminum casting procedure: layout, manufacturing, product evaluation, and product testing.
(https://www.awwwards.com/a1castcmpny/)The foundry needs to likewise have a proven record of delivering exceptional items that satisfy or surpass consumer expectations. Quality assurance must likewise go to the top of your checklist when selecting a light weight aluminum foundry. By collaborating with a qualified factory that follows the standards for quality assurance, you can protect the stability of your item and ensure it satisfies your requirements.
Excitement About Alcast Company
By selecting a firm that supplies solutions that fulfill or surpass your product demands, you can be sure that your task will certainly be finished with miraculous precision and effectiveness. Specific aluminum foundries concentrate on particular kinds of making procedures or casting approaches. Different components call for various production techniques to cast light weight aluminum, such as sand spreading or die casting.
Die spreading is the name provided to the process of creating intricate metal elements with use of molds of the part, likewise called passes away. The process makes use of non-ferrous steels which do not include iron, such as light weight aluminum, zinc and magnesium, because of the desirable homes of the metals such as low weight, greater conductivity, non-magnetic conductivity and resistance to corrosion.
Some Ideas on Alcast Company You Should Know
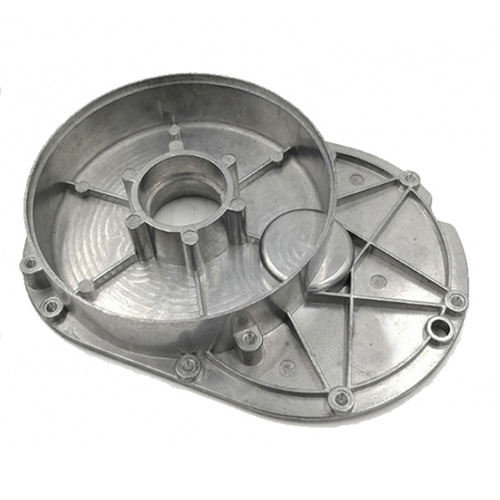
No matter the sub-process, the die spreading process can be damaged down into six actions. After the purity of the alloy is examined, passes away are created. To prepare the needs spreading, it is very important that the passes away are clean, so that no deposit from previous productions stay. After cleansing, the ejection lubrication is related to the die to ensure a smooth release.
The pure metal, likewise referred to as ingot, is contributed to the furnace and kept at the molten temperature of the steel, which is after that moved to the shot chamber and injected into the die (Foundry). The pressure is then preserved as the steel strengthens. As soon as the steel strengthens, the cooling procedure starts
Everything about Alcast Company
The thicker the wall surface of the component, the longer the cooling time as a result of the amount of indoor steel that likewise needs to cool down. After the part is completely cooled, the die cuts in half open and an ejection device pushes the component out. Following the ejection, the die is shut for the next injection cycle.
The flash is the extra product that is cast throughout the procedure. This must be cut off utilizing a trim tool to leave simply the primary component. Deburring eliminates the smaller sized items, called burrs, after the trimming process. Ultimately, the element is polished, or burnished, to offer it a smooth finish.
The Single Strategy To Use For Alcast Company
Today, top manufacturers use x-ray screening to see the whole interior of parts without cutting right into them. To get to the ended up item, there are three primary alloys utilized as die casting material to choose from: zinc, light weight aluminum and magnesium.
Zinc is just one of one of the most used alloys for die casting due to its lower cost of resources. It's also one of the stronger and stable metals. And also, it has excellent electrical and thermal conductivity. Its corrosion resistance also enables the parts to be durable, and it is among the much more castable alloys because of its lower melting point.
The 15-Second Trick For Alcast Company
As pointed out, this alloy is one of one of the most frequently used, yet produces will, at times, pick aluminum over zinc due to light weight aluminum's manufacturing benefits. Light weight aluminum is extremely economical and one of read what he said the more flexible alloys. Light weight aluminum is utilized for a number of different items and industries anything from home window frames to aerospace products.